Cellcycle, one of the UK’s leading lithium battery recycling companies, has today announced the development of a novel and groundbreaking direct recycling process for lithium-ion batteries.
This innovative method uses environmentally friendly, green solvents to sustainably separate the binder, cathode active material (CAM), and aluminium foil from battery production scrap, providing a streamlined, energy-efficient approach to recycling that could potentially eliminate the need for additional processes such as hydrometallurgy and pyrometallurgy.
By reducing carbon emissions and maintaining the integrity of the recovered materials, this process sets a new standard in sustainable battery recycling.
Through this new innovative process, the team were able to successfully recover over 95% of the cathode active material from NMC 532 lithium battery production scrap using green solvents. However, unlike other recycling methods that rely on extreme temperatures as high as 600 degrees, the team at Cellcycle were able to achieve these results whilst keeping temperatures below 80.
This demonstrates its capability to recover battery-grade materials directly from manufacturing scrap, ensuring they can be seamlessly reintegrated into the production process. Such efficiency is crucial for addressing the growing challenge of battery production waste as the industry continues to expand.
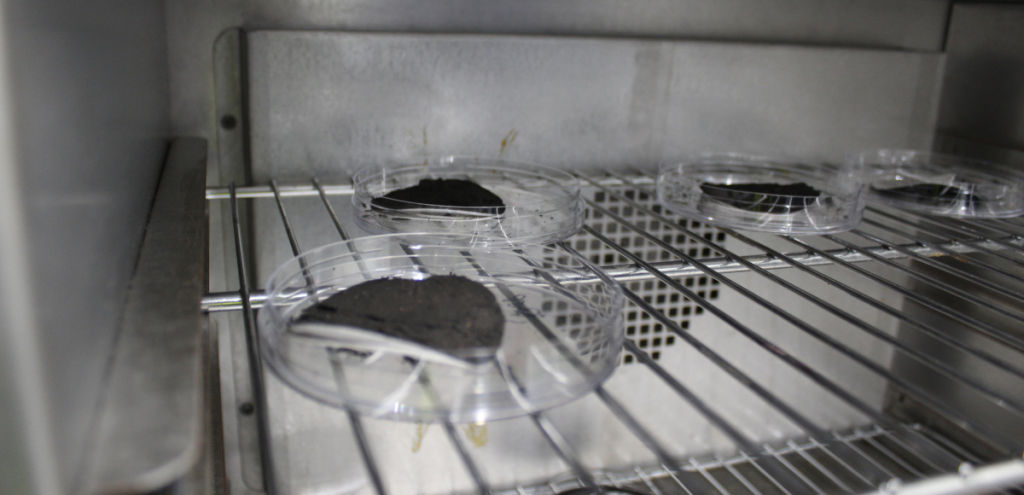
Raouf Hosseini, Associate Professor at Cellcycle commented, “This innovation marks a vital step forward for the battery industry, particularly here in the UK. At present, the country lacks any commercial scale refining capability, yet the demand for critical mineral recovery will grow significantly as more gigafactories become operational in the coming years. Our process addresses this pressing challenge by recovering high-quality materials in a sustainable manner, paving the way for a more resilient and environmentally responsible battery supply chain.”
Direct recycling is essential for the future of battery sustainability, enabling the recovery of high-quality materials without the environmental costs associated with traditional methods. Compared to other direct recycling approaches, which often depend on energy-intensive techniques to remove binders, Cellcycle’s process operates under milder conditions, further reducing its environmental footprint and energy demands.
“This achievement is a testament to our commitment to innovation and environmental stewardship,” said Jonathan Regan, Head of Technical at Cellcycle. “We’re not just tackling today’s waste challenges but laying the groundwork for a circular battery economy that benefits both industry and the planet.”
As demand for lithium-ion batteries continues to surge across electric vehicles, renewable energy, and consumer electronics, ensuring a closed-loop supply chain is critical. By recovering and reintegrating essential materials into manufacturing, Cellcycle’s solution aligns with Europe’s goals for sustainable industrial practices and a greener future.
This development reflects Cellcycle’s broader strategy to lead in comprehensive lithium battery solutions. With a focus on innovative green technologies, the company is dedicated to managing waste responsibly and supporting the UK and Europe in building a robust circular economy for lithium batteries.
For further information, please contact: Max Nagle
Marketing and Communications Manager
Cellcycle, the SER Group
max@cellcycle.co.uk